At present, more than 95% of semiconductor components worldwide are based on the first generation semiconductor material silicon as the basic functional material. However, with the rise of new applications such as electric vehicles and 5G, silicon-based semiconductors are limited by the physical properties of silicon materials and have performance bottlenecks that are not easy to break through. Therefore, third-generation semiconductor materials represented by gallium nitride (GaN) and silicon carbide (SiC) have begun to receive attention.
In the third-generation semiconductor materials, SiC has the characteristics of large bandgap width, high breakdown electric field, high saturation electron drift velocity, and high thermal conductivity, which can be applied to high voltage environments above 1200 volts. Therefore, it has obvious advantages in harsh environments.
Meanwhile, SiC crystal is an ideal substrate material for GaN based devices, such as LEDs and LDs (laser diodes), due to its high matching lattice constant, thermal expansion coefficient, and good thermal conductivity with the epitaxial layer material GaN. Therefore, SiC crystal material has become an indispensable substrate material in the field of semiconductor lighting technology.
Among them, SiC substrate processing technology is an important foundation for device fabrication. The quality and accuracy of its surface processing directly affect the quality of epitaxial thin films and the performance of devices. Therefore, in its application, it is required that the chip surface be ultra smooth, defect free, and damage free, with surface roughness values below the nanometer level.
However, due to the high hardness, brittleness, good wear resistance, and extremely stable chemical properties of SiC crystals, the processing of SiC chips has become very difficult.
The ultra precision machining process of SiC single crystal wafers mainly involves the following processes according to their processing sequence: directional cutting, grinding (coarse grinding, fine grinding), polishing (mechanical polishing), and ultra precision polishing (chemical mechanical polishing).
01 Cutting
Cutting is the process of cutting SiC crystal rods into thin crystal slices along a certain direction. Cutting SiC crystal rods into chips with low warpage, uniform thickness, and low cutting loss is crucial for subsequent grinding and polishing. Compared with traditional inner and outer circle cutting, multi wire cutting has the advantages of high cutting speed, high processing accuracy, high efficiency, and long service life, and has been widely used for efficient cutting of chips.
The principle of multi wire cutting technology: Multi wire cutting technology is to cut the ingot into cutting pieces with a flat surface and uniform thickness according to a certain crystal orientation, in order to facilitate subsequent grinding and processing.
The basic principle is that high-quality steel wire moves back and forth at high speed on the surface of the ingot, and the diamond particles in the cutting fluid attached to the steel wire cause severe friction on the ingot, causing the material to fracture and fall off from the surface of the matrix, achieving the cutting effect.
02 Grinding
The purpose of grinding is to remove the knife marks and surface damage layer on the SiC slice surface caused by the cutting process. Due to the high hardness of SiC, it is necessary to use high hardness abrasives (such as boron carbide or diamond powder) to grind the crystal surface of SiC slices during the grinding process. Grinding can be divided into coarse grinding and fine grinding according to different processes.
Rough grinding is mainly used to remove cutting marks and deteriorated layers caused by cutting, and to use larger abrasive particles to improve processing efficiency. Fine grinding is mainly used to remove the surface damage layer left by rough grinding, improve surface smoothness, and control the surface shape and thickness of the chip, which is conducive to subsequent polishing. Therefore, finer abrasive particles are used to grind the chip.
Due to the low fracture toughness of SiC, it is prone to cracking during the grinding process, making it very difficult to grind SiC chips. Effective grinding requires selecting appropriate grinding parameters to achieve maximum material removal rate and control surface integrity.
03 Rough throwing
Rough polishing mainly adopts mechanical polishing method, using smaller particle size hard abrasives such as B4C, diamond, etc., to repair the surface of the chip.
Used to remove residual stress layers and mechanical damage layers during the grinding process, improve surface flatness and quality, efficiently complete material removal, and lay the foundation for subsequent ultra precision polishing.
04 Ultra precision polishing
Through traditional rough polishing process, SiC chips are mechanically polished using diamond or B4C polishing solution with small particle size. The flatness of the chip surface is greatly improved, but there are many scratches on the processed surface, as well as deep residual stress layer and mechanical damage layer.
In order to further improve the surface quality of chips, enhance surface roughness and flatness, and ensure that their surface quality characteristic parameters meet the accuracy requirements in subsequent processing, ultra precision polishing is a crucial step in SiC surface processing.
With the development of ultra precision polishing technology, currently, the main ultra precision polishing methods suitable for SiC single crystal wafers include mechanical grinding, magneto rheological polishing, ion beam polishing, chemical mechanical polishing, etc. Among them, chemical mechanical polishing (CMP) technology is currently the most effective method for achieving global planarization of SiC wafers.
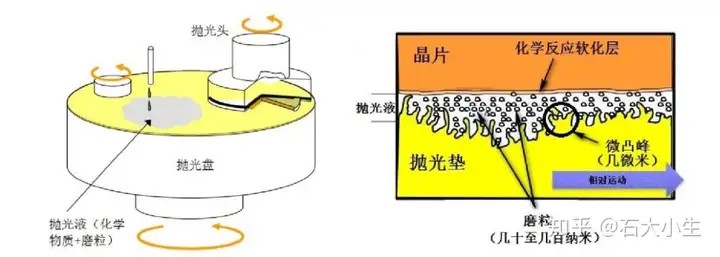
Chemical mechanical polishing is the process of removing and flattening the surface material of a workpiece through the synergistic effect of chemical corrosion and mechanical wear. The chip undergoes chemical oxidation under the action of polishing solution, forming a chemical reaction layer on the surface, which is then removed by the mechanical action of abrasive particles.
Due to the multidisciplinary knowledge involved in chemical mechanical polishing technology, such as chemistry, physics, friction, mechanics, and materials science, there are many factors that affect its polishing effect, mainly including polishing fluid (abrasive particles, oxidants, pH value, additives, etc.), polishing pad (hardness, elasticity, surface morphology, etc.), and polishing parameters (polishing pressure, polishing head/polishing disc speed, polishing fluid flow rate, etc.).
Among them, polishing solution is the core of chemical mechanical polishing technology, so its impact is decisive. Generally speaking, CMP polishing solution is composed of abrasive particles, oxidants, deionized water, and additives. Therefore, the polishing effect can be regulated from these factors, such as the type of abrasive, abrasive particle size, and abrasive particle concentration.
At present, the oxidants commonly used in CMP polishing solutions are mainly H2O2 and KMnO4, and the abrasive particles mainly include SiO2, CeO2, and Al2O3. Feng Yue et al. used a modified silicon solution with a wavelength of 30-135nm to perform precision polishing treatment on SiC chips, and found that the residual damage layer after the rough polishing process could be completely removed, thus obtaining high-quality polished surfaces.