Recently, Vicino and the Hefei Municipal Government signed a memorandum of cooperation, in which both parties will work together to promote the investment, construction, and production operation of Vicino's 8.6th generation AMOLED production line project. This is the second panel manufacturer in China to explicitly join this battle. The signing and implementation of this project has attracted market attention.
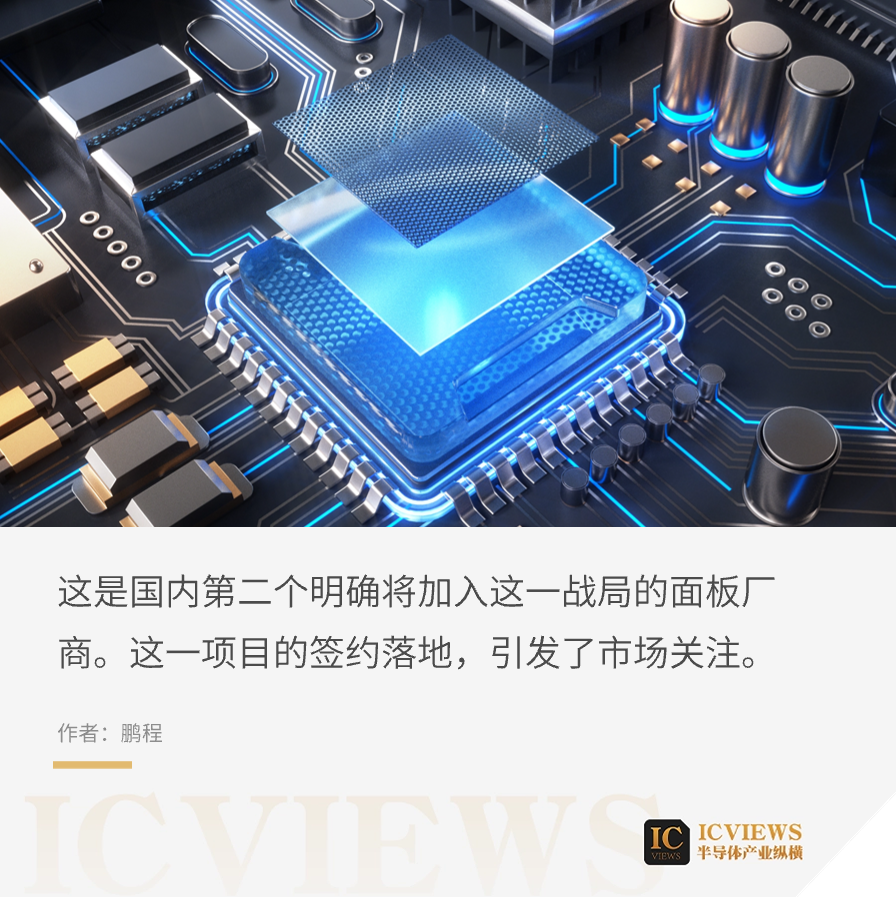
OLED (Organic Light Emitting Diode), also known as organic light-emitting diode, is a current type organic light-emitting device. The principle is to use organic semiconductor materials and luminescent materials to generate light through the injection and recombination of charge carriers (electrons and holes) driven by an electric field. Specifically, OLED devices include ITO transparent electrodes and metal electrodes, which serve as the anode and cathode of the device, respectively. Under a certain voltage drive, electrons and holes are injected into the electron and hole transport layer from the cathode and anode, respectively, and then migrate to the luminescent layer where they meet to form excitons and excite luminescent molecules, which emit visible light through radiation relaxation.
OLED displays have many advantages compared to traditional LCD screens, including being lighter, thinner, higher brightness, lower power consumption, faster response, higher clarity, better flexibility, and higher luminous efficiency. These characteristics make OLED very prominent in meeting the needs of flat panel display applications, especially in high-end electronic products such as smartphones and televisions.
The research on OLED originated in the mid to late 20th century. In 1979, Dr. C.W. Tang, a Chinese American scientist working at Kodak in the United States, unexpectedly discovered that organic batteries emit light in the dark, laying the foundation for OLED research. Dr. Deng is therefore known as the "father of OLED".
In 1987, American scientists Austin Frechetti and Steven van Simpson discovered the first effective material for organic light-emitting diodes, which is considered an important milestone in OLED research. In the same year, Dr. Wang Genyang and colleagues from Kodak successfully used a double-layer organic structure similar to a semiconductor PN junction to create a low-voltage and high-efficiency light emitter for the first time, laying the foundation for the production of OLED displays. Kodak's first OLED double-layer device showcases the excellent performance of OLED, including thinner, blacker, and faster response.
In 1997, OLED was the first commercially produced and used in automotive audio systems by Pioneer Japan worldwide. In the early days, the only market for OLED was in car displays, which gradually expanded to include mobile phones, PDAs, cameras, and other fields. Around 2010, Samsung in South Korea broke through the large-scale high-quality production technology of 5th to 6th generation line and hard screen OLEDs.
In 2009, major manufacturers began to shift their focus to AMOLED, resulting in AMOLED's output value surpassing PMOLED for the first time. In 2013, manufacturers such as LGD and SMD launched 55 inch OLED TVs, marking a breakthrough for OLED in the field of large-sized displays. The 2017 Apple 10th Anniversary iPhone X features an AMOLED screen. With the continuous maturity of OLED technology and the expansion of market size, OLED production capacity is gradually increasing.
OLED only took 16 years from its first commercial application to the successful launch of a 55 inch TV screen, while LCD took 32 years to go through this process, indicating the rapid development of the global OLED industry.
OLED 8th generation technology is an important technological advancement, mainly aimed at the production of medium to large-sized panels.
Generation 8.6 refers to "generation lines", and several generations of lines mainly refer to the size of the substrate. The larger the size, the more large-sized screens can be produced, or more small-sized screens can be cut out in one process to meet the needs of large screens or greatly improve production efficiency.
The 8th generation OLED technology is mainly aimed at the market of mid to large-sized IT products such as tablets and laptops, and improves production efficiency and economy by using larger glass substrates. The glass substrate size corresponding to the 8.6th generation OLED production line is 2290 * 2620mm.
At present, the domestic OLED panel production lines are mainly based on 6th generation and below generation lines, which are mainly used for small and medium-sized LCD substrate glass. The technical difficulty of medium and large-sized substrates is high, and domestic manufacturers are further increasing their investment in new product research and development. The 8.6 and 8.5 generation OLED production lines are gradually starting mass production, laying the foundation for the large-scale development of the medium and large-sized substrate glass industry.
Japan and South Korea have already engaged in a technological competition in the field of OLED, especially in the 8th generation OLED FMM (Fine Metal Mask). DNP, a Japanese printing company, and Poongwon Precision, a Korean material supplier, are actively expanding production capacity and introducing new technologies.
In addition, Samsung Display has jointly developed the 8th generation full cut vertical evaporator with Japan's Aifa Technology, and plans to start mass production of the 8th generation OLED for IT from 2024. BOE has mastered the FMM free lithography technology and has made attempts on both QLED and OLED.
The leap from mass production of the 6th generation OLED FMM to commercialization of the 8th generation OLED FMM poses significant technological and material challenges. With the gradual rise of OLED TVs and displays, the market demand for high-precision and large-sized ultra fine metal mask FMMs will also increase significantly.
However, the 8th generation OLED production line is more economical compared to the 6th generation line, which helps improve production efficiency and reduce costs. The 8.6th generation OLED production line for IT products typically uses Oxide substrates instead of LTPS substrates, and uses the RGB evaporation process, which is more mature than printing OLED or QD-OLED methods.
High generation OLEDs will become the main trend in the future development of OLEDs.
From a global perspective, both China and South Korea are intensifying their layout of the 8.6-generation AMOLED production lines.
Before and after 2021, Samsung and LG successively proposed the plan to build an 8-generation OLED IT professional line. It is inevitable that the demand for panels for Apple's next-generation devices such as laptops, desktops, and tablets was immediately targeted by potential major customers. For more than two years, Samsung, represented by the largest display device supplier group of Apple, and Korean panel industry have invested a lot of research in the 8th generation OLED IT equipment and process routes.
Last April, Samsung Display Co. invested 4.1 trillion Korean won (approximately RMB 21.525 billion) to establish a mass production system for advanced OLED panels in South Korea. In March of this year, Samsung Display announced that it had started building a new 8.6-generation IT organic light-emitting diode (OLED) production line, a strategic initiative taken by the company to consolidate its leadership position in the global flat panel display market. This production line consists of two 7.5K production lines per month (15K per month) in a double stacked series connection.
According to the plan, Samsung Display will transform the existing L8 production line to A6 production line at its Eshan Central factory, producing 8.6-generation OLED panels for IT equipment in addition to smartphones. This will be Samsung's sixth OLED production line for displays, with plans to install major equipment this year and begin large-scale production in 2026.
In February of this year, there were rumors that LG Display would continue to build its 8.6 generation (2250 x 2600mm) IT AMOLED production line. The company has negotiated supply agreements with equipment manufacturers. It is reported that this project is scheduled to be officially announced in the second half of this year, with a production capacity of 7500-15000 substrates per month. LG will utilize its existing P10 factory and equipment to reduce costs, which means its expansion plan for WOLED TV panel production capacity will be postponed. It is expected that the demand for IT AMOLED displays will increase significantly in the future.
Domestic panel giants are also unwilling to fall behind. BOE has opened its first domestic 8.6-generation OLED panel production line in Chengdu, which is the first and second global 8.6-generation AMOLED production line in China, with a total investment of 63 billion yuan. The goal is to mass produce 8.6 generations of OLED panels by 2026.
According to official disclosure, the project of BOE covers an area of 925200 square meters and the registered capital of the project company is 38 billion yuan. Among them, BOE raised 19.994 billion yuan, the first phase of heavy production raised 9.003 billion yuan, and the electronics company raised 9.003 billion yuan. The difference between the total project investment and registered capital was partially resolved through external financing by the project company. The G8.6 production line constructed by this project will further improve the preparation process of backboards and OLED light-emitting devices on the basis of the existing G6 OLED production line technology. Products using this technology have lower power consumption and longer lifespan compared to the previous generation products.
At the end of April this year, there were also rumors that TCL Huaxing was about to enter the 8.6 generation OLED market. However, TCL Huaxing's parent company TCL Technology has announced a clarification of this news. TCL Huaxing CEO Zhao Jun also stated in an interview earlier this month, "We do not have a clear timetable to build an 8.6-generation OLED production line. The decision on this matter depends on many aspects, including internal technical readiness, market competition, and industry technology iteration trends. We will comprehensively consider these factors, evaluate them at an appropriate time, and make corresponding decisions. However, there is indeed no clear timetable at the moment."
The emerging display industry is standing at the intersection of technological revolution and industrial upgrading. Building a higher generation line is the trend of the times and a strategic opportunity that must be seized. At present, the progress of the 8.6-generation OLED production line in China and South Korea is quite competitive.
As the market landscape for LCD and small-sized OLEDs becomes increasingly clear, the progress of the target large-sized 8.6-generation OLED line has become a focus of attention in the display industry. Whether mainstream manufacturers invest, when they start production, and how they progress will all affect the future competitive landscape of the entire industry.
As South Korean companies exit the LCD industry, the competition in the display industry between China and South Korea focuses on traditional strengths of South Korean companies such as OLED and emerging display technologies such as Micro LED. Despite South Korean companies having several years of first mover advantage and technological accumulation in OLED technology, the continuous catch-up of Chinese display companies in recent years is also bridging the gap.
In the traditional OLED application market dominated by smartphones, Chinese display companies are in a catching up position. In the emerging OLED application markets such as laptops and tablets, display companies in China and South Korea are basically on the same starting line in terms of technology. And this is precisely the battlefield of next-generation OLEDs.
In terms of next-generation OLEDs, although domestic manufacturers lack experience, Korean companies including Samsung are not entirely experienced. Because it is the first time that various manufacturers in China and South Korea have made the 8.6 generation line.
Currently, the planned production capacity of two domestic manufacturers has reached 64K/month, while the official Samsung production capacity announced by the Korean manufacturer is 15K/month. In this dimension, China has already surpassed South Korea in terms of production capacity layout. In terms of technology or investment speed, Samsung is expected to be faster because it will be mass-produced next year or the year after, while BOE will only be able to mass produce after 2026, which will be slower.
Thanks to the huge volume of electronic products and massive capital investment in the Chinese market, OLED is expected to replicate the reversal of the LCD industry in the Chinese and Korean corporate markets. One of the key factors is the breakthrough in domestic equipment, materials, and process technology.
"Currently, Korean factories are the main suppliers of large-sized OLEDs, and the addition of BOE (BOE) and the layout of the next-generation OLED production line indicate a further reshaping of the OLED panel supply pattern. It is also expected to accelerate the penetration of OLEDs in the IT industry, promote product upgrades, introduce new technologies, and improve the upstream and downstream systems of the supply chain." Wei Tianhao, Intermediate Research Manager of Oviruwo, said.
CICC Research points out that currently, key upstream equipment and materials for OLEDs are still dominated by overseas manufacturers, and domestic manufacturers are expected to gradually break through the monopoly of overseas manufacturers in some mid to late stage equipment, organic terminal materials, mask plates, and driver chips. Omdia data also points out that the localization rate of AMOLED panels in the domestic market continues to increase. For example, in 2023, the total production capacity of TFT backplanes used for AMOLED in Chinese Mainland will rise to 43%, while the proportion of Samsung in South Korea will fall to 41%. This means that in the field of AMOLED panels, domestic manufacturers and Korean manufacturers have been evenly matched, and even Chinese manufacturers have exceeded Korean manufacturers in some fields.
However, South Korean companies and governments are also intensifying their layout in an attempt to win this competition.
According to South Korean media reports, the South Korean government will concentrate on investing 420 billion Korean won in scientific research and development (R&D) funds to upgrade the eighth generation OLED production technology for IT and the tenth generation OLED production technology for televisions. At the same time, South Korea will also provide more tax and financing support for OLED higher generation lines. The industry in our country is also concerned that South Korea will use its relationship with the Japanese industry to form an "industrial alliance" under the mediation of the United States to compete in the upstream materials, equipment, and high generation line construction of OLEDs in our country, similar to the linkage between Europe, America, Japan, and South Korea in the fields of semiconductors and lithography machines.
At present, both Samsung and BOE A claim that their 8.6-generation line will be mass-produced in 26 years, and the progress of the military competition for higher-generation OLED production lines at home and abroad is difficult to distinguish. On the battlefield of 8.6 generation OLED technology for IT, it remains to be seen who can take the lead.